How to Choose Right control Valve Bonnet for your Application?
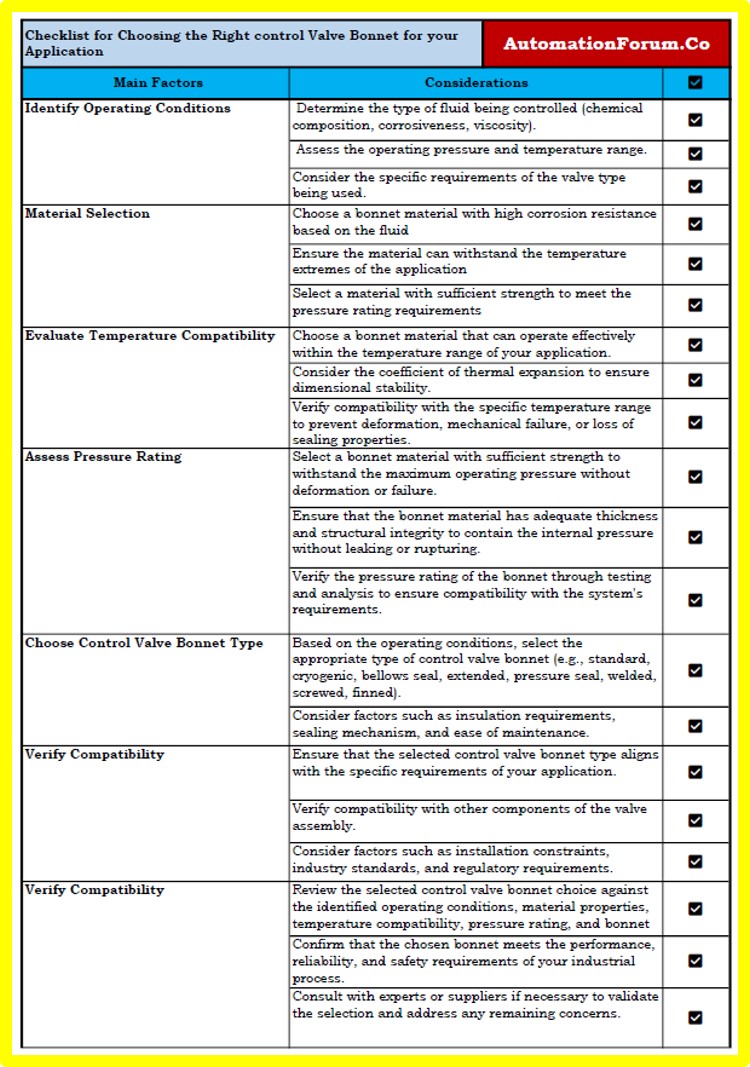
- Functions of Control Valve Bonnets
- Choose Right control Valve Bonnet for your Application
- Factor No.1: Understanding Operating Conditions
- Factor No.2: Material Selection
- Factor No.3: Temperature Compatibility
- Factor No.4: Pressure Rating
- Factor No.5: Sealing Properties
- Factor No.6: Types Of Control Valve Bonnets
- What are the different types of bonnets in control valves?
- Checklist for Choosing the Right control Valve Bonnet for your Application
What is Control Valve Bonnet?
The control valve bonnet is a protective component that covers the top of a control valve body, safeguarding internal components and maintaining optimal operating conditions
Functions of Control Valve Bonnets
Control valve bonnets serve several essential functions in the operation of control valves:
Protection
- Bonnets protect internal valve components, such as the actuator, stem, and packing, from environmental elements, corrosion, and mechanical damage.
Sealing
- Bonnets provide a sealing interface between the valve body and the valve trim, ensuring leak-tight operation and preventing fluid loss or contamination.
Temperature Management
- Certain bonnet types, such as cryogenic and thermal bonnets, help manage temperature variations within the valve, ensuring consistent performance in extreme temperature conditions.
Accessibility
- Bonnets facilitate easy access to internal components for maintenance, inspection, and repair, minimizing downtime and ensuring efficient operation.
Choose Right control Valve Bonnet for your Application
- Choosing the right valve bonnet for your application is crucial for ensuring optimal performance, reliability, and safety of your industrial processes.
- A valve bonnet serves several important functions, including providing a seal to prevent leakage, housing internal components, and facilitating maintenance and repair.
- We’ll go into more detail in this thorough explanation about the things to take into account when choosing the right valve bonnet for your particular application.

Factor No.1: Understanding Operating Conditions
Type of Fluid
- Consider the chemical composition, corrosiveness, viscosity, and other properties of the fluid being controlled by the valve.
- Certain materials may be more compatible with specific fluids, while others may corrode or degrade over time.
Operating Pressure and Temperature
- Evaluate the maximum and minimum pressure and temperature conditions that the valve and bonnet will be subjected to during operation.
- Ensure that the chosen bonnet material can withstand these conditions without deformation or failure.
Valve Type
- Different valve types, such as globe valves, gate valves, ball valves, and butterfly valves, require different bonnet designs to accommodate their unique operating mechanisms and sealing requirements.
- Choose a bonnet type that is compatible with the specific valve type being used.
Factor No.2: Material Selection
- Material selection for valve bonnets is critical to ensure reliable performance, longevity, and safety in various industrial applications.
- Here’s a detailed look at each aspect of material selection:
Corrosion Resistance
Corrosion is a common issue in industrial environments where valves are exposed to aggressive fluids. Selecting a bonnet material with high corrosion resistance is essential to prevent degradation and maintain the integrity of the valve assembly.
Commonly used materials for corrosion-resistant bonnets include:
- Stainless steel alloys, such as 316 stainless steel, offer excellent corrosion resistance, making them suitable for a wide range of applications, including those involving corrosive fluids like acids, alkalis, and seawater.
- These exotic alloys provide superior resistance to corrosion, oxidation, and high-temperature environments. They are commonly used in demanding applications where standard materials may fail due to aggressive chemical exposure.
Factor No.3: Temperature Compatibility
Valve bonnets must withstand the temperature extremes of the operating environment without experiencing deformation, mechanical failure, or loss of sealing properties.
- Choose a bonnet material that can operate effectively within the temperature range of your application, whether it involves extreme heat or cryogenic temperatures.
- Consider the coefficient of thermal expansion of the bonnet material to ensure dimensional stability and prevent issues such as thermal cycling-induced stress and leakage.
Factor No.4: Pressure Rating
The bonnet material must meet the pressure rating requirements of the system to ensure safe and leak-free operation under varying pressure conditions.
Factors to consider include:
- Select a bonnet material with sufficient strength to withstand the maximum operating pressure without deformation or failure. Carbon steel and alloy steel are commonly used for high-pressure applications due to their excellent mechanical properties.
- Ensure that the bonnet material has adequate thickness and structural integrity to contain the internal pressure without rupturing or leaking. Pressure testing and analysis can help verify the suitability of the selected material for the intended pressure range.
Factor No.5: Sealing Properties
- Choose a bonnet material that is compatible with the valve seat material to facilitate a tight and durable seal. Proper material selection can prevent issues such as galvanic corrosion and chemical incompatibility that may compromise sealing integrity.
- Ensure that the surface finish of the bonnet mating surfaces is smooth and free of defects to promote effective sealing with gaskets or seals. Surface treatments such as polishing or coating may be applied to enhance sealing properties.
Factor No.6: Types Of Control Valve Bonnets
What are the different types of bonnets in control valves?
- Control valve bonnets play a crucial role in ensuring the proper functioning of control valves across various industrial applications.
- Each type of control valve bonnet is tailored to specific operational requirements, ensuring reliable and efficient performance across a wide range of industrial applications. Understanding the characteristics and functions of these bonnets is essential for selecting the most suitable option for a particular application.
- Here are the common types of control valve bonnets:
Standard Bonnet
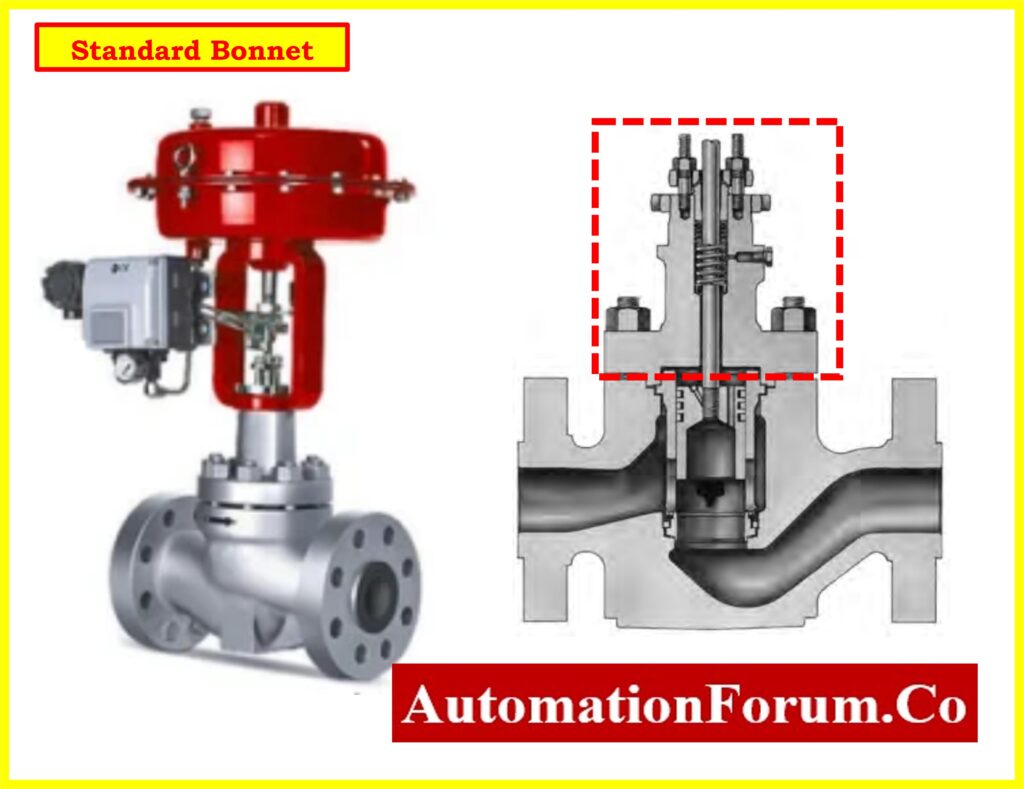
- Standard, also known as bolted bonnets, are the most prevalent type of control valve bonnets.
- They comprise a straightforward cover bolted onto the valve body.
- These bonnets offer fundamental protection to internal components and facilitate easy access for maintenance and repair tasks.
- The most commonly used type of valve bonnet and Works well in typical operating conditions.
- Suitable for everyday applications and provides a tight seal to prevent leaks.
Cryogenic Bonnet
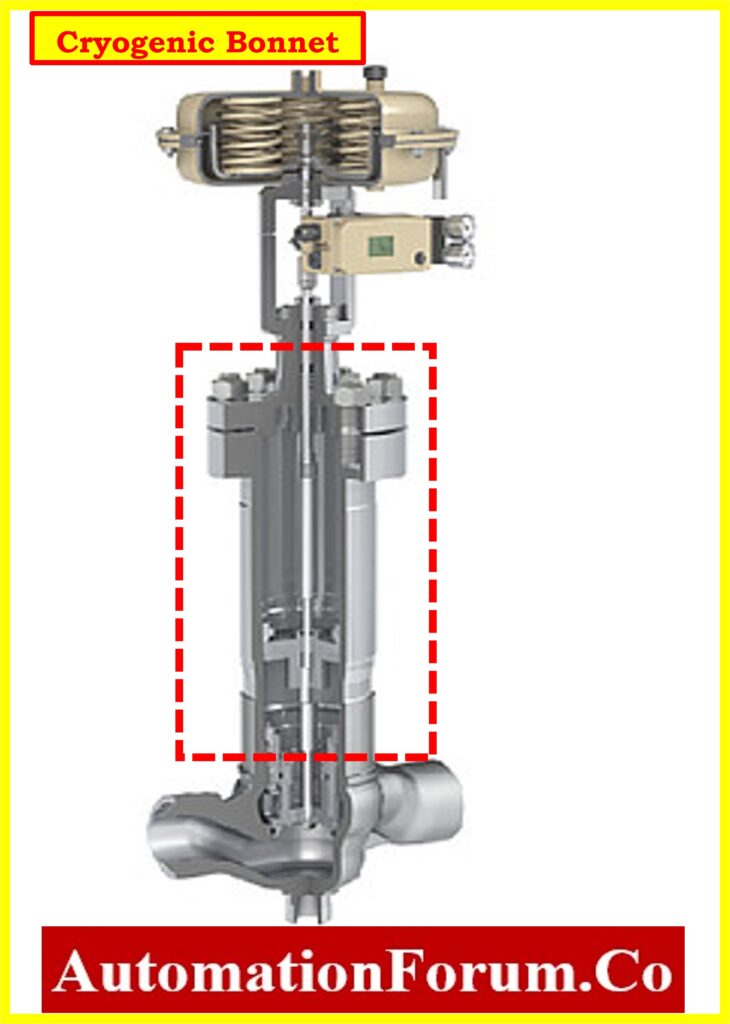
- Engineered to withstand extremely low temperatures, cryogenic bonnets are insulated to prevent freezing of valve components and maintain fluid integrity in cryogenic environments.
- They are essential for reliable operation in applications where temperatures reach ultra-low levels.
Bellows Seal Bonnet
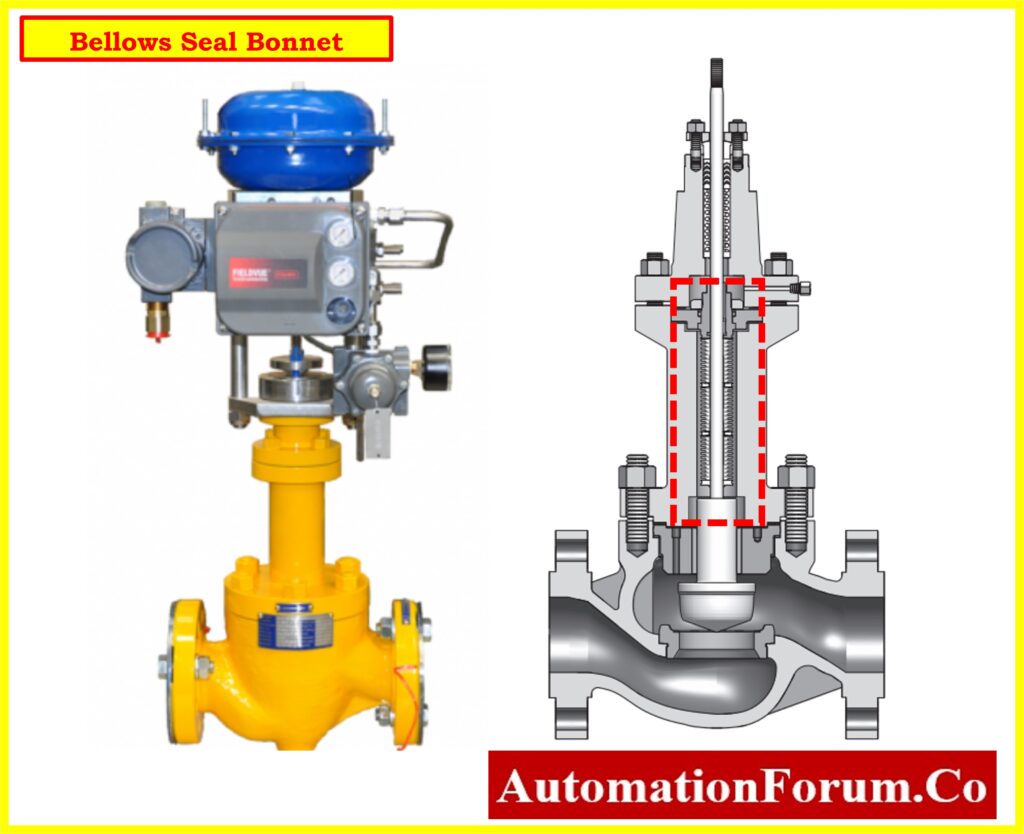
- Bellows seal bonnets utilize a bellows seal mechanism to provide superior sealing against leakage.
- They are particularly suitable for applications involving corrosive or hazardous fluids, where tight sealing is essential for safety and environmental protection.
Extended Bonnet
- Extended bonnets are designed for use in applications with high temperatures.
- Their elongated design keeps the actuator and packing components away from the high-temperature fluid stream, thus preventing damage or malfunction caused by exposure to excessive heat.
- Also known as a long bonnet ball valve.
- Tailored for high-temperature and high-pressure applications.
- Offers extended length to accommodate insulation and protect packing from extreme temperatures.
Bolted Bonnets
- These bonnets are secured to the valve body using bolts and are relatively easy to remove for maintenance and repair.
- Bolted bonnets provide a strong and reliable seal and are suitable for a wide range of applications, including high-pressure and high-temperature environments.
Pressure Seal Bonnets
- Designed for high-pressure applications, pressure seal bonnets use a self-sealing mechanism that becomes tighter as the internal pressure increases.
- These bonnets are often used in gate valves and require specialized tools for installation and removal.
Welded Bonnets
- Welded bonnets are permanently attached to the valve body through welding, providing a robust and leak-proof seal.
- While they offer excellent reliability and durability, welded bonnets can be challenging to repair or replace and are best suited for applications with minimal maintenance requirements.
Screwed Bonnets
- Screwed bonnets feature threads that allow them to be screwed onto the valve body.
- They are commonly used in smaller valves and low-pressure applications where frequent maintenance is not required.
Finned Bonnet
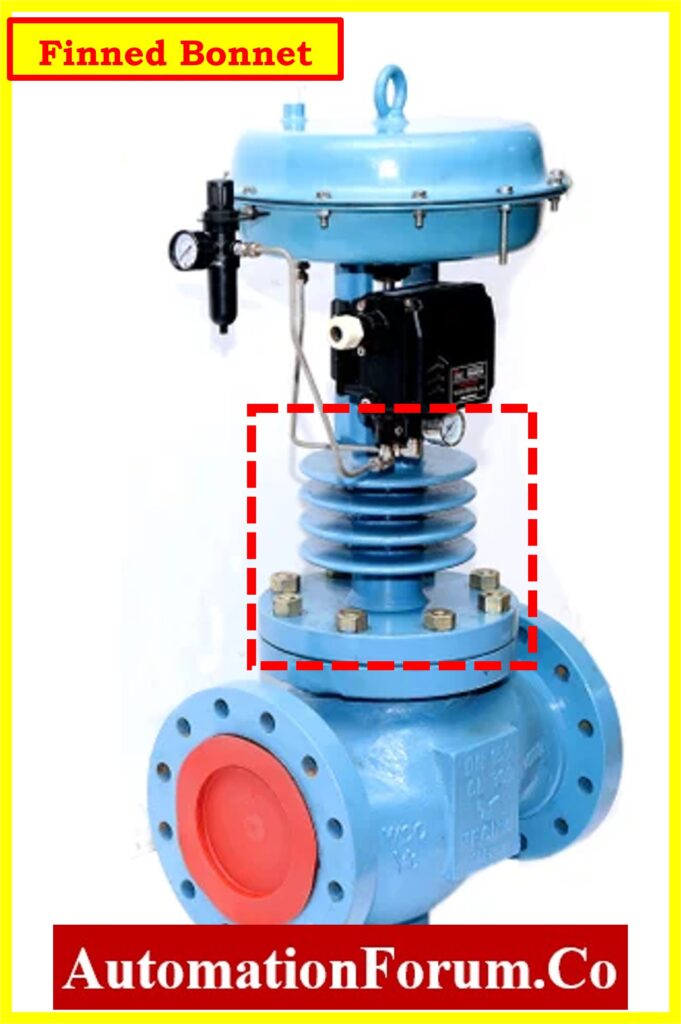
- A finned bonnet, featuring extended fins, is chosen for applications needing efficient heat dissipation. Ideal for high-temperature services like steam systems, it prevents overheating of valve components.
- With increased surface area, it improves heat transfer, extending valve longevity and reliability.
- Common in power generation and petrochemical industries, it’s also beneficial in cryogenic applications, managing thermal stresses effectively.
Checklist for Choosing the Right control Valve Bonnet for your Application
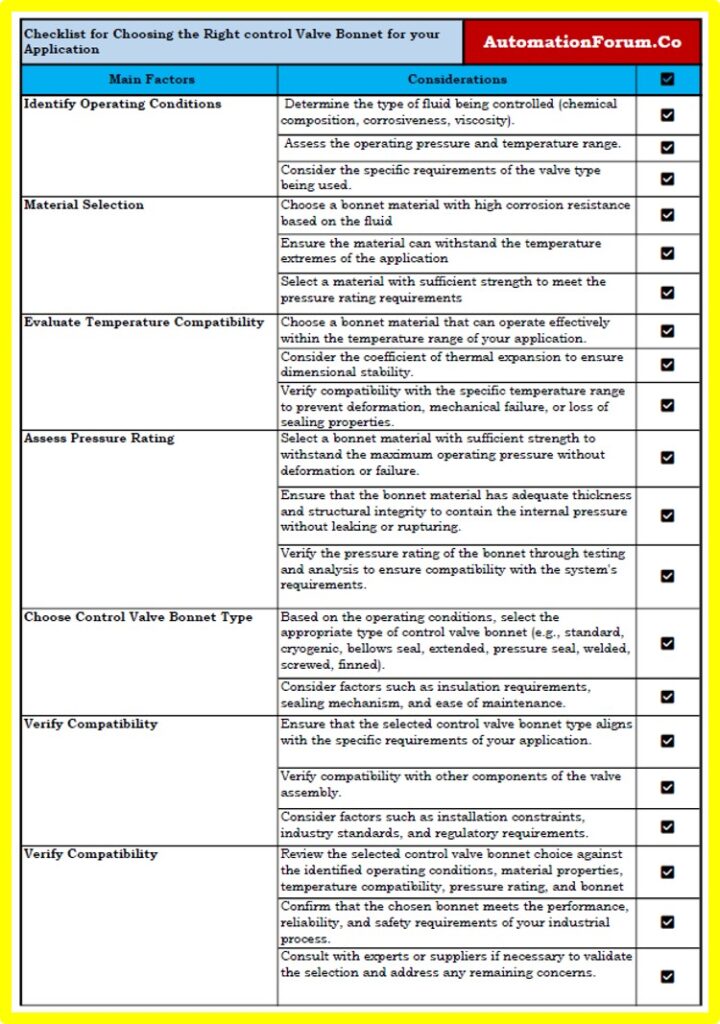
Following these sequential Downloadable excel Check list will help ensure that you choose the right control valve bonnet for your specific application, considering all relevant factors and requirements.
FAQ
What is the Difference Between a Valve Body and a Valve Bonnet?
The valve body houses the internal components and serves as the primary structural component of the valve, while the valve bonnet covers the top of the valve body, providing access for maintenance and sealing the internal components.
Click here for Control Valves in Process Industries: A Collection of In-Depth Articles