Control Valve Hunting due to Valve Positioner: Troubleshooting
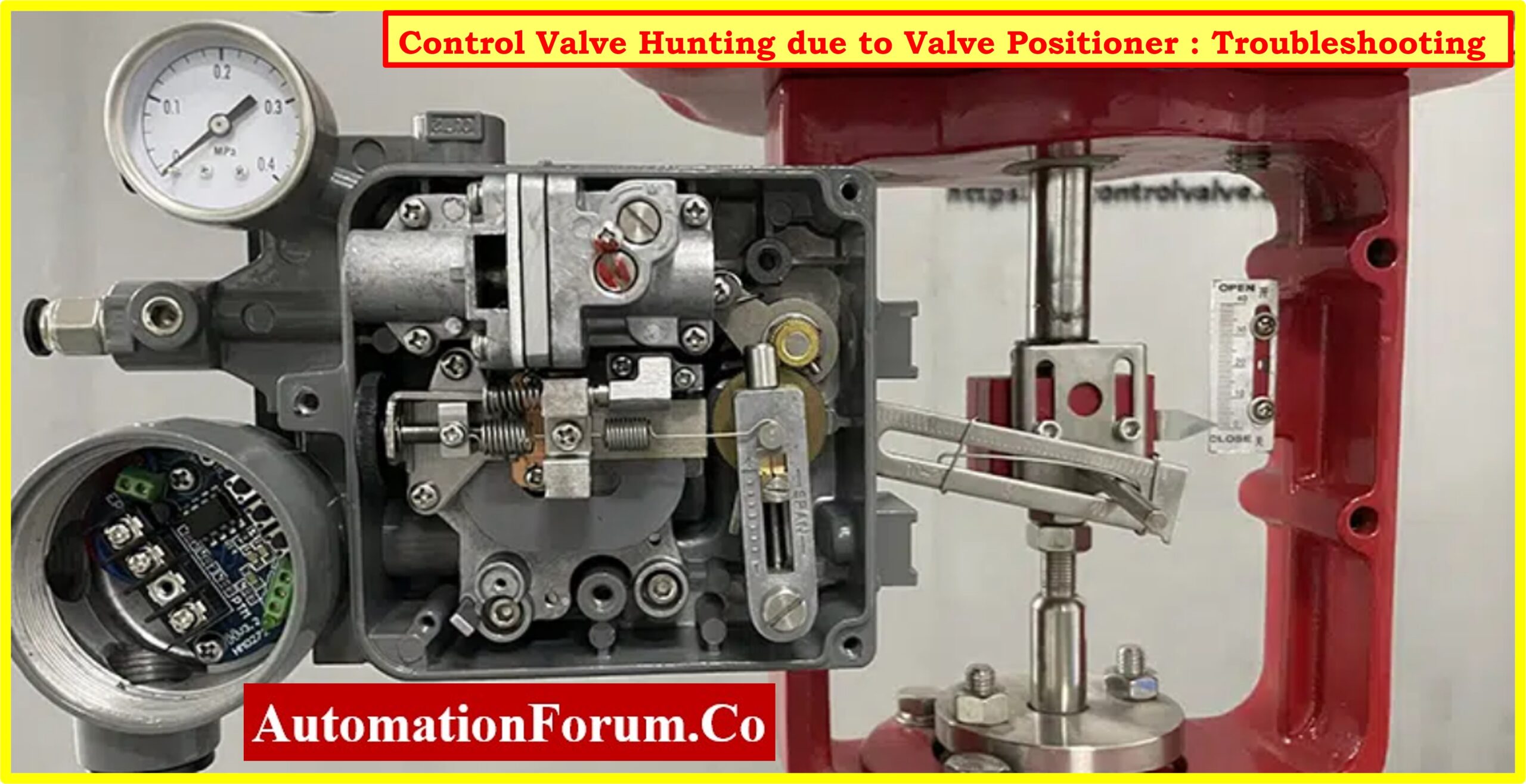
- Understanding the Control Valve Positioner
- Identifying Problems with the Control Valve Positioner
- Root Cause Analysis: Moisture Ingress
- Case Study: Resolving Moisture-Related Hunting
- Case Study : Spool Valve Wear and Cleaning
- Avoiding Control Valve Positioner Breakdown
- Troubleshooting Summary
- What does a Valve Hunting Mean?
- What is hunting in control systems?
- In the dynamic environment of industrial processes, control valve positioners are critical to achieving precision and reliability. However, when hunting concerns occur, they could cause considerable operating challenges.
- In this detailed troubleshooting guide, we will go deeper into the complexities of control valve positioners, identifying typical issues, doing root cause analysis, and providing actionable solutions.
Understanding the Control Valve Positioner
Role of Valve Positioners:
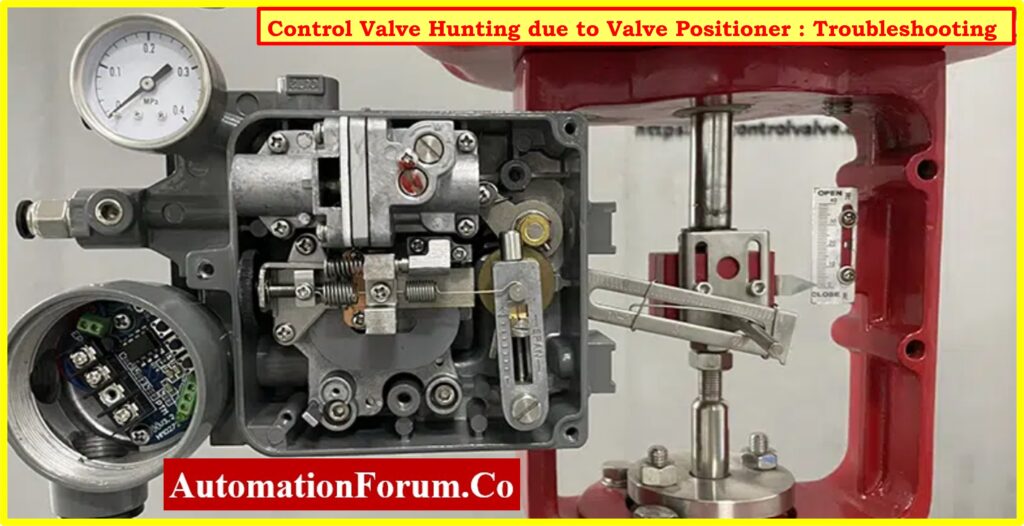
- Control valve positioners act as the bridge between control devices and valves, ensuring the seamless execution of setpoints.
- To have more control over a process, valve positioners are used.
- The operator sends a signal to the positioner indicating precisely how much flow should move through the valve, and specific set points are displayed.
- However, valve positioners can occasionally have trouble locating their intended location. There are several possible causes for this unreliable motion, which is referred to as “hunting.”
- Hunting is the result of a deviation from the intended operation and is characterized by erratic valve movements.
- This is how an electro-pneumatic positioner operate as like Valve Positioner I/P Converter receives a 4-20mADC Control Signal from your control device, and converts it to a linear 3-15 PSI Output for the positioner.
- The positioner’s milliamperage is shown by the 4–20mA symbol; 4 milliamps represents a closed valve and 20mA represents a completely open valve.
- The milliamperage needed to run the positioner is directly correlated with the PSI.
- For instance, the actuator receives 9 PSI and opens the valve to 50% when the positioner milliamperage reads 12mA.
Symptoms of Hunting
- The effects of hunting are important, as it has an effect on the efficiency of processes and the stability of systems, and it has the potential to cause damage that is permanent.
- When it comes to initiating intervention, early recognition of these indicators is essential.
Identifying Problems with the Control Valve Positioner
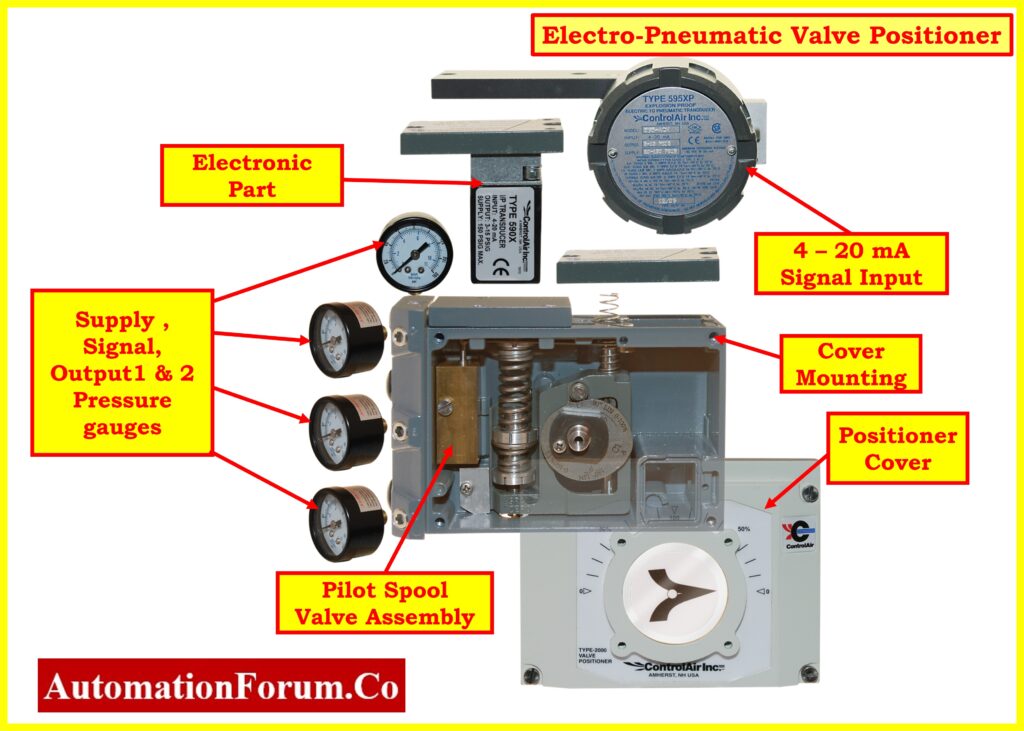
Instrument Air Supply
- Making sure the instrument air supply pressure meets the necessary specifications is a vital step.
- Performance that is less than optimal can be the result of deviations.
Inspection for Air Leakage
- It is essential to do thorough inspections for air leaks in the actuator body and instrument air tube.
- The control valve’s overall responsiveness may be impaired by leaks.
Inspection of the Positioner Cover
- Removing the cover exposes possible problems including moisture penetration.
- This is a critical step in determining the root cause of hunting.
Click here to carry out Inspection of Control Valve
Root Cause Analysis: Moisture Ingress
- The control valve hunting was caused by moisture entering into the positioner. The positioner’s internal parts were harmed by this moisture.
- The positioner was promptly changed by the Instrumentation professional.
- Following that, the valve was auto-calibrated, and after stroke checking, it was given to the operations team.
Click here to carry out Calibration of Control Valve Positioner
Click here to carry out Calibration procedure for Control Valve
Click here to carry out Stroke Checking of Control Valve
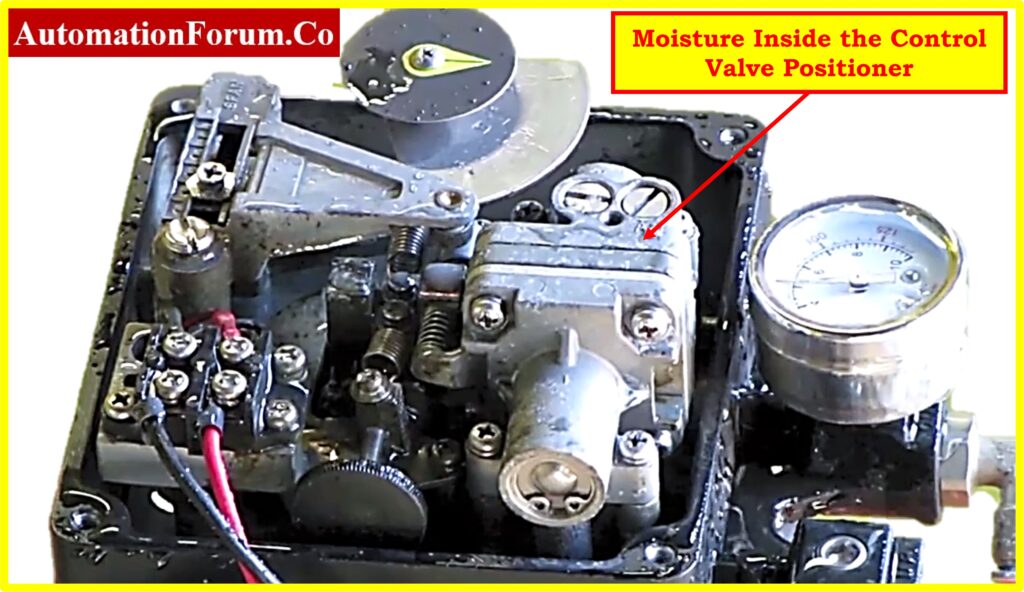
Moisture in Positioner
- Moisture intrusion is dangerous since it might cause internal component damage and hunting as a result.
- To mitigate this risk, protective solutions like canopies and aluminum tape are considered.
Preventive Measures
- It is essential to have preventative measures in place, particularly in areas that are likely to experience wetness.
- Canopies, gasket application, and various methods for protecting equipment are outlined.
Case Study: Resolving Moisture-Related Hunting
- After doing a more thorough examination, the instrumentation crew discovered a minor but significant element that was causing the moisture intrusion: a missing bolt.
- This missing bolt left a small opening in the positioner’s cover, which allowed moisture to enter even with the silastic applied correctly.
- This weakness was made worse by the other three bolts that pulled the cover inside.
- Moisture entered the system through the missing bolt, highlighting the importance of a thorough inspection during troubleshooting.
- Not only was it a mechanical error, but it also highlighted the importance of taking an in-depth look at every element, including the less important ones.
Case Study : Spool Valve Wear and Cleaning
Critical Role of Spool Valve
- Understanding the criticality of the spool valve in pneumatic valve positioners is essential.
- The wear and tear of the spool valve can significantly impact control system efficiency.
- A component known as a spool valve is located inside the base pneumatic valve positioner.
- It is a forced-balanced device with a cam characteristics that is easy to calibrate and maintain. It is also essential to the positioner’s functionality.
- Air pressure should be permitted to decide the spool’s position as it moves freely inside the block.
- There is wear and tear possible in the gold plating of the spool valve. Both regular use and contaminated air can be the cause of this.
- As a result, the spool piece has a tendency to stick within the block, which increases the risk of air pressure building up and exceeding the set point. Control over the valve is lost, and its position becomes erratic.
Spool Valve Cleaning Procedures
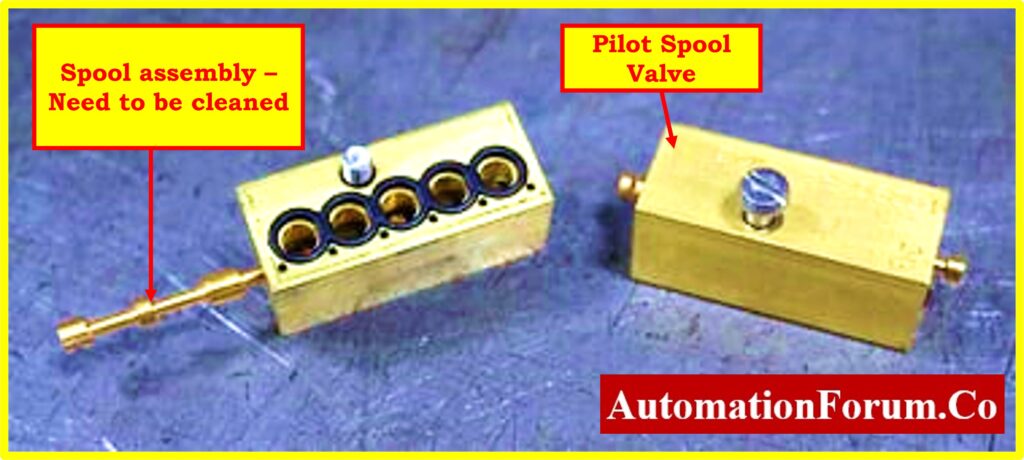
- Use air to empty the spool valve in order to clean it. Use a cloth to clean it if air isn’t accessible.
- Use a soft cloth, such as a pipe cleaner, to clean the inside of the spool block. However, do not clean the spool piece with WD40 or any other oil-based lubricant.
- Efficient cleaning methods for the spool valve are discussed, highlighting the importance of regular maintenance.
Click here do Maintenance on Struck Control Valve
Avoiding Control Valve Positioner Breakdown
This type of problem, along with many others, can be resolved by following the guidelines listed below.
Regular Inspection
- Round up the missing parts during inspection. Bolts, silastic, monsoon tape, loose coverings, and missing canopies are examples of this.
Preventive Maintenance
- Every instrument’s cover should be opened during the PM (Preventive Maintenance) task.
- This will reveal the instrument’s internal state to us. Reinstall the cover, being careful to oil any bolts or threads that require it.
- Additionally, this will help to prolong the life of bolts and threads, which are subject to aging-related reductions.
- Because to corrosion, the bolts can occasionally break while being opened. Because the bolts will always be lubricated, opening them in every PM job will help to partially eliminate this corrosion. The fact that monsoon or silastic tape will be reapplied is another benefit.
- It can take many hours to pull and replace the valve. It only takes less than five minutes to clean the spool valve or replace it if needed.
Click here do Preventive Maintenance Procedure for Control Valve
Pending Jobs Monitoring
- The importance of monitoring and addressing pending jobs, especially related to missing bolts, is emphasized. Proactive intervention can prevent future issues.
Troubleshooting Summary
- In industrial processes, control valve positioners are essential, but hunting problems can cause irregular valve movements, which can interrupt operations.
- The troubleshooting strategy places a high value on preventative measures, systematic root cause investigation, and early symptom recognition.
- Valve positioners are used to control processes by following setpoints; hence, early intervention is necessary to identify symptoms.
- Examining the positioner cover, checking for leaks in the actuator and air tube, and verifying the instrument air supply are the tasks involved in troubleshooting.
- The consequence of a missing bolt is highlighted in a case study on moisture penetration, illustrating the importance of thorough inspections.
- An additional case study emphasizes how crucial spool valve maintenance is to preventing wear and tear that lowers control system effectiveness.
- In addition to routine inspections and preventive maintenance, protective techniques, gaskets, and canopies should be used in regions that are prone to moisture.
- This comprehensive guide offers instrumentation specialists the necessary troubleshooting techniques, preventative measures, and practical case studies for the best possible control system reliability and efficiency.
Click here more Collection of In-Depth Articles about Control Valve
Frequently Asked Questions
What does a Valve Hunting Mean?
- “Valve hunting” refers to the situation where a valve continuously oscillates or hunts around the desired setpoint due to rapid on/off cycles.
- This often occurs when the control system is improperly tuned, causing instability and excessive wear on the valve actuator.
- To address this issue, control systems incorporate a dead band or hysteresis mechanism, creating a range around the setpoint where no action is taken.
- This helps stabilize the system, preventing constant switching of the valve between on and off states and reducing wear on valve components. Proper tuning of control system parameters is essential for achieving stable and efficient process control, minimizing valve hunting.
Click here for What are the main causes of control valve hunting?
What is hunting in control systems?
Hunting in control systems occurs when the system, responding to a sudden signal or transient, overcorrects itself by initially moving in one direction and then overcorrecting in the opposite direction. This phenomenon is undesirable for system stability. To counteract hunting, damping is commonly added to the system to slow down its response, preventing excessive overshoots or overcorrections.