Industrial Automation
Burnout Function of a Temperature Transmitter with an example
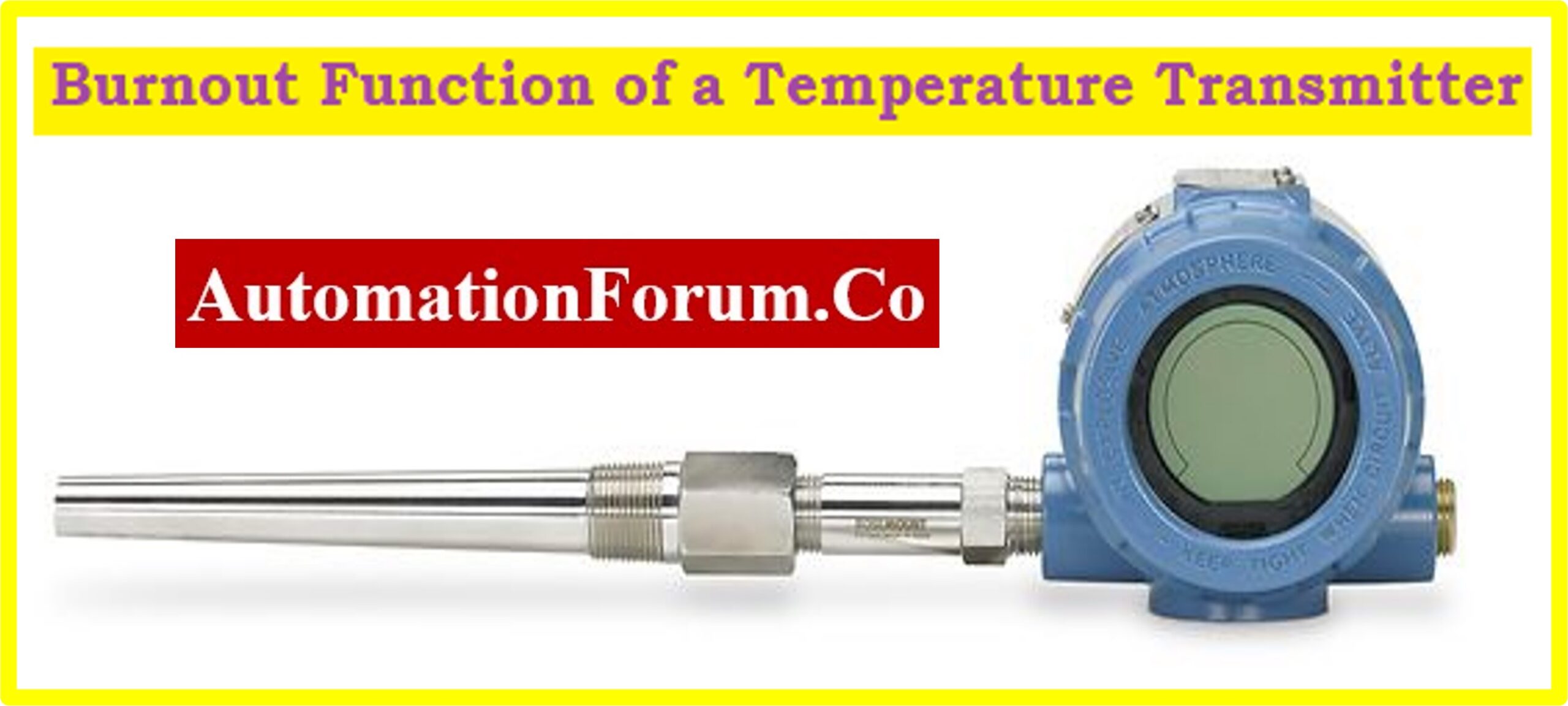
Table of Contents
- What happens if the temperature sensor opens maximum resistance? Do you get the exact temperature reading?
- How a temperature transmitter does determine sensor failure?
- Have you ever considered what happens when an RTD or thermocouple fails?
- What is Transmitter Burnout?
- What is the Temperature Burnout Feature? What basically is a burnt-out thermocouple?
- What is a Burnt-Out Thermocouple?
- What is the purpose of a burnout switch in the context of an RTD or thermocouple transmitter?
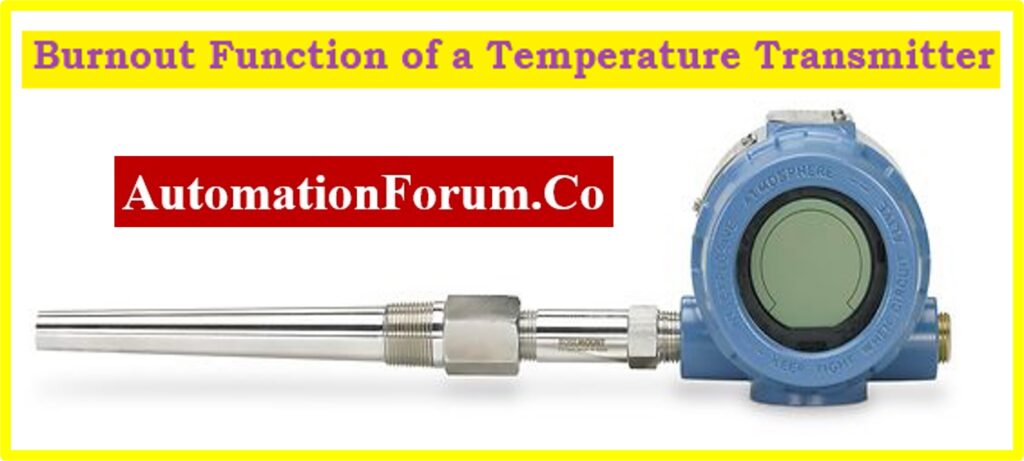
In this article, we will study the Temperature Transmitter Burnout Function.
- When a transmitter or sensor stops working, regardless of whether it’s a short circuit or an open circuit, a specified current signal that is pre-configured in the transmitter is communicated.
- The burnout function in a temperature transmitter is a critical feature that saves both the plant and the equipment.
- Temperature transmitters receive input signals from sensors such as RTDs and Thermocouples.
- The voltage signal is converted by the transmitter into a 4-20 mA current signal for transmission to a PLC or SCADA.
- Depending on the signal requirements of the processor, the transmitter can also convert the sensor signal into an FF signal or any other type of signal.
- We modify the variables in the transmitter for improved system control and troubleshooting.
- Device tag, primary variable, secondary variable, Tertiary variable, range of all variables, LRV, URV, Engineering units, Damping, Transfer function (Linear/Square root), Display setting, and so on are among the parameters.
- The temperature transmitter’s “Burnout Function” parameter is also programmed or configured.
- A temperature transmitter transforms the output voltage received by the sensor into a current signal or other types of signal.
What happens if the temperature sensor opens maximum resistance? Do you get the exact temperature reading?
- The actual temperature reading may not be available at this time.
- If a process interlocks with high temperature, the plant trips, making huge production losses.
- If no process fault occurs the plant should not trip under this condition.
- In the second case, If RTD resistance shorts out. RTD interprets -242.021 °C temperature at zero resistance.
- At this time, if the process temperature rises too high, the PLC will not output a Temperature High signal, and the plant keeps functioning. This may result in undesirable incidents such as explosions and fires.
- The solution to the issues mentioned is to set up or configure the Burnout function in the temperature transmitter.
- The Burnout function supports the control room operator in identifying the root cause of high or low temperature.
- If it is due to the process temperature rising too high or because of sensor failures.
- When a transmitter identifies probe failure (detector shorted or an open circuit), it generates the pre-configured current value. At the transmitter end, we could configure the low, high, or another significant measure as required.
How a temperature transmitter does determine sensor failure?
- In compliance with NAMUR NE 43 when the loop current becomes less than 3.6 mA or rises above 21 mA, the transmitter generates a sensor fault.
- Before presenting the sensor malfunction problem, the transmitter supervises the current for at least 4 seconds.
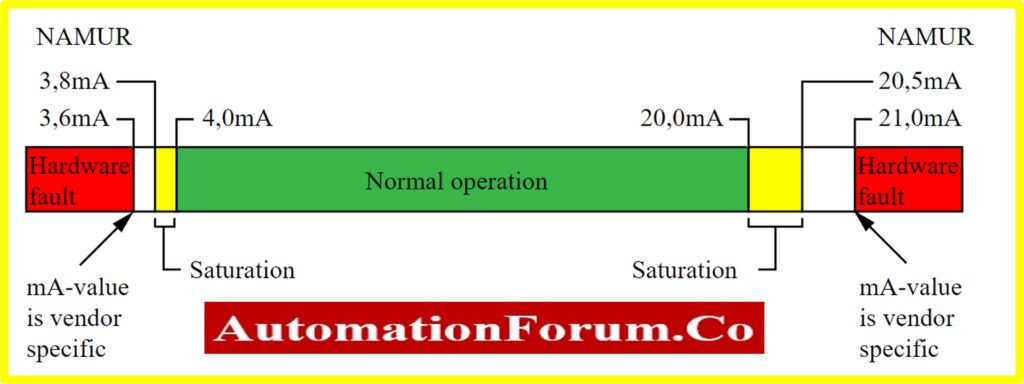
- The configuration of high current and low current in the event of a sensor fault is determined by the kind of process, and it is essential to verify the required specifications before setting.
- Just after the activation of the burnout function in the temperature transmitter, the instrument engineer or instrument technician must observe & record the configuration in the record book.
- Note that any activity being performed on a temperature transmitter with a burnout feature must be bypassed via PLC or DCS before going ahead.
- The Transmitter’s role is simple, it receives sensor input and converts it into system-understandable values, such as a 4-20 mA signal, an FF signal, or any other type of signal based on the instrument type.
- Various process parameters, like Device Tag, Primary variable, Secondary variable, Tertiary variable, Variable Range, Lower Range Values, Upper Range Values, Engineering units, Damping factor, Linear or Square root Transfer function, & Display setting, are important parameters in temperature transmitter, the Burnout Function, must be designed during the transmitter’s completion of the plant project.
Have you ever considered what happens when an RTD or thermocouple fails?
Let us consider one example.
- If a Resistance Temperature Detector fails in the field for any purpose and the resistance becomes too high (open connection), the process will trip in the presence of a high-temperature interlock.
- Because of this trip, the plant could be shut down, leading to an interruption of production.
- Consider another situation in which the RTD stops working and induces a short circuit.
- When the resistance of the PT100 RTD sensor goes to zero, the equivalent temperature is -242.021 °C.
- However, in real-time, suppose the temperature in the plant rises, and if it surpasses the critical temperature value, a massive explosion may occur, resulting in an incident.
To solve these problems, the burnout function must always be accomplished.
- When a transmitter detects sensor failure like a short circuit or an open circuit, a defined pre-configured current signal is transmitted through the transmitter.
- Based on necessity, we can configure a low value, a high value, or some other defined value, or the previous state’s high value is 20 mA and the low value is 4 mA in a 4-20 mA loop.
- The key question now is how the temperature transmitter detects the failure of the actual sensor, since it may create erroneous readings at this time.
- By investigating the procedure, you can determine what configurations should be incorporated in the transmitter burnout function.
- The burnout function must be clearly specified if configured in the temperature transmitter, mentioned somewhere written in the field or a list of such transmitters is formatted.
- When an instrumentation engineer or technician visits for any activity on the temperature transmitter, the required bypass has to be accomplished in the DCS or ESD system.
What is Transmitter Burnout?
Transmitter burnout denotes failure for unknown reasons. Burnout direction represents whether you’d like your transmitter to output maximum value when it fails (i.e. burnout in high direction) or minimum value when it fails (i.e. burnout in low direction) (i.e. burnout in low direction)
What is the Temperature Burnout Feature? What basically is a burnt-out thermocouple?
- The thermocouple burn-out function is commonly used in a temperature control system that incorporates a thermocouple input.
- The controller loses the input signal if the thermocouple burns out.
- This is equivalent to the measured temperature dropping significantly.
What is a Burnt-Out Thermocouple?
- The thermocouple burn-out function is generally used in a temperature control system with a thermocouple input.
- If the thermocouple goes badly, the controller tends to lose the input signal.
- This is similar to the measured temperature dropping very low.
What is the purpose of a burnout switch in the context of an RTD or thermocouple transmitter?
The Burnout Mode Switch lets you choose between upscale and downscale burnout modes. Upscale burnout is accomplished by applying a small current (provided by the instrument’s internal milli-voltage source) to the thermocouple’s input.