Types of Oxygen Analyzers: Applications and Measurement Methods
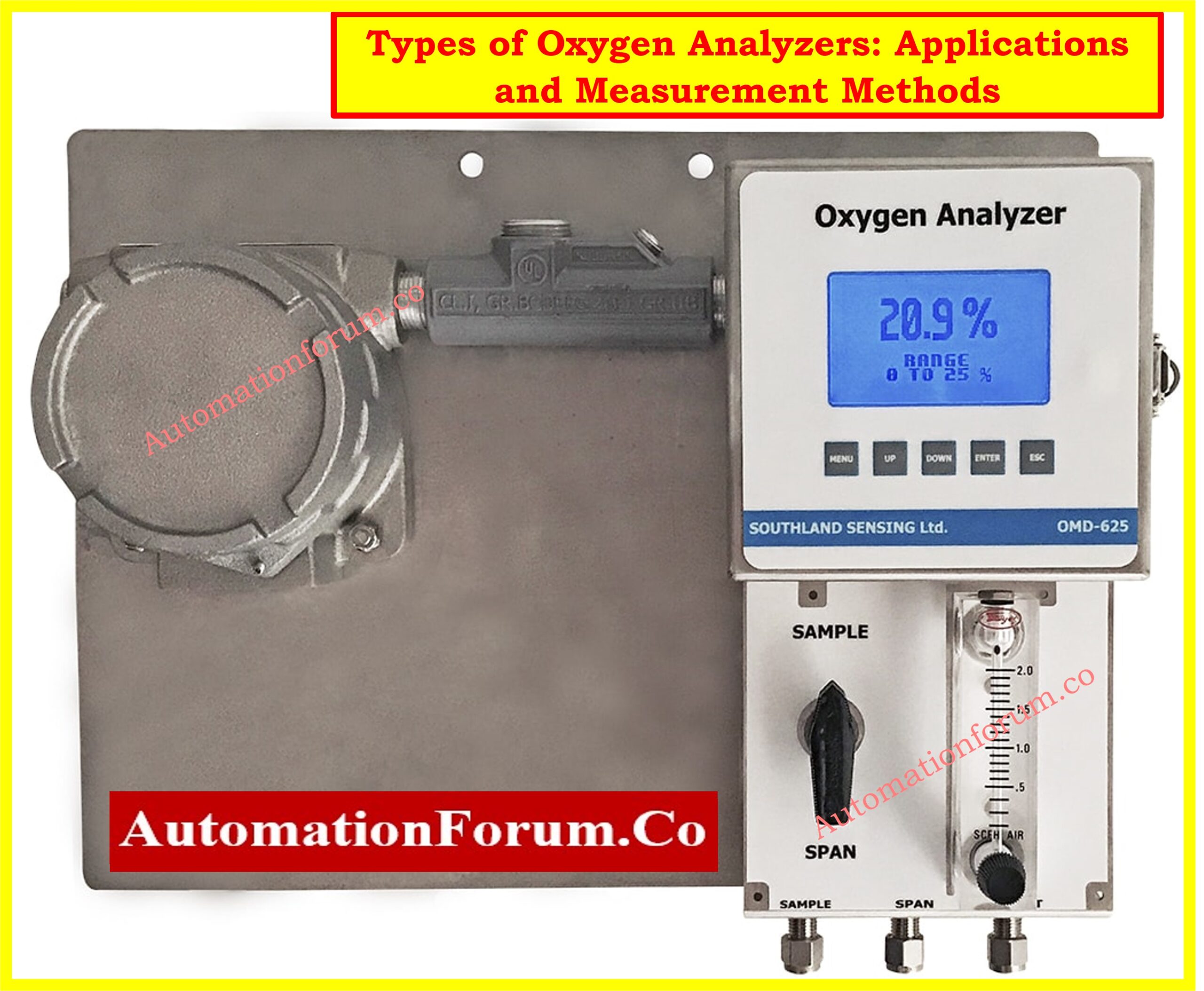
- What is an Oxygen Analyzer?
- Stack Gas Oxygen Analyzers
- Inert Gas Oxygen Analyzers
- Applications of Oxygen Analyzers
- Types of Oxygen Analyzers
- Oxygen Analysis Methods
- Zirconia Type Measurement System: Concentration Cell System
- Zirconia Type Measurement System: Limiting Current Type
- Magnetic Type Measurement System: Paramagnetic System
- Optical Type: Tunable Diode Laser Measurement System
- Electrochemical Type: Galvanic Cell Type
- Application Examples for Each Oxygen Analyzer
What is an Oxygen Analyzer?
- Oxygen analyzers are essential instruments used to measure oxygen levels in various environments, ensuring safety and efficiency across diverse industries.
- They come in two main types: stack gas analyzers and inert gas analyzers.
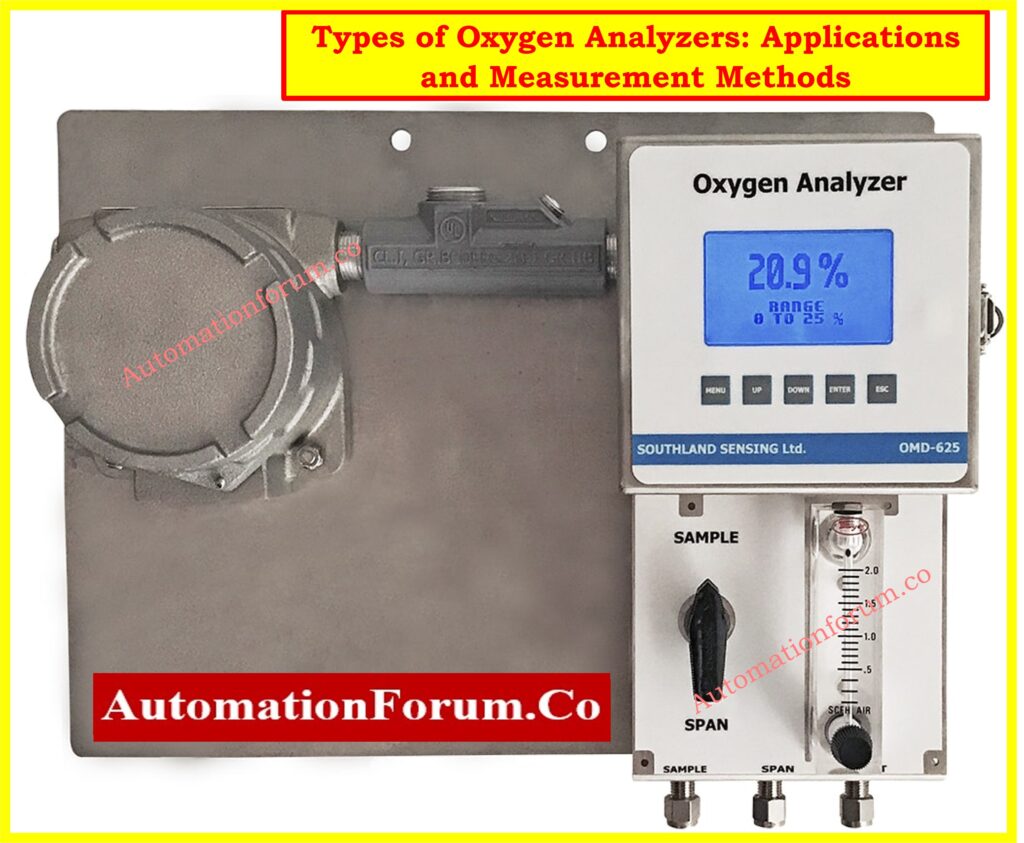
Stack Gas Oxygen Analyzers
- These devices measure oxygen levels in exhaust gasses post-combustion, crucial for controlling fuel-to-air ratios in processes like boiler operation.
- Proper oxygen levels optimize combustion efficiency, preventing energy loss.
Inert Gas Oxygen Analyzers
- These analyzers measure oxygen content in inert gasses used to displace oxygen in void spaces.
- Low oxygen levels are essential to maintain inert atmospheres, especially in processes like energy production from landfill or biogas.
Applications of Oxygen Analyzers
Because they can reliably and efficiently monitor and control oxygen levels, oxygen analyzers are a valuable tool for a wide range of applications. The following is a more in-depth examination of each of these applications:
Landfill Gas, Biogas, Syngas Production
- In these processes, organic materials are decomposed in an oxygen-free (anaerobic) environment, producing gases like methane (in landfill and biogas) or a mixture of carbon monoxide and hydrogen (in syngas).
- Oxygen analyzers are essential for maintaining anaerobic conditions by monitoring and controlling the oxygen levels.
- This ensures optimal gas production and minimizes the risk of unwanted reactions or emissions. The produced gases can then be utilized as renewable energy sources, contributing to sustainability efforts.
Gas Plants, Transmission Lines, and Gathering Systems
- Oxygen presence in gas infrastructure indicates potential leaks, which can lead to safety hazards and economic losses.
- Oxygen analyzers play a crucial role in detecting leaks by continuously monitoring oxygen levels within gas plants, transmission lines, and gathering systems.
- Rapid detection of oxygen ingress allows operators to identify and address leaks promptly, preventing accidents, environmental damage, and loss of valuable resources.
Industrial Processes
- Industries depends on precise oxygen level monitoring to ensure the efficiency, quality, and safety of manufacturing processes.
- For example, in aerospace manufacturing, where components are often produced under controlled atmospheres to prevent oxidation, oxygen analyzers help maintain the required oxygen levels.
- Similarly, in electronics manufacturing, oxygen analyzers ensure the purity of inert gases used during soldering or semiconductor fabrication processes. Continuous monitoring of oxygen levels enables companies to optimize production processes, enhance product quality, and comply with regulatory standards.
Safety
- Handling cryogenically liquefied gasses or pressurized gas cylinders poses inherent safety risks, including the potential for oxygen depletion in the surrounding environment.
- Oxygen analyzers are critical for monitoring oxygen levels in such environments to detect leaks or oxygen depletion caused by gas release.
- Early detection of leaks or oxygen depletion helps prevent potential hazards, ensuring the safety and well-being of workers.
Types of Oxygen Analyzers
There are four primary types of oxygen analyzers, namely:
Trace Oxygen Analyzer:
- Known for its precision, this type is favored in natural gas and industrial applications where even minute variations in oxygen levels matter significantly for optimal performance and safety.
Portable Oxygen Analyzer:
- This handy device is designed for on-the-spot oxygen level checks, offering flexibility in environments where fixed analyzers are impractical or unavailable, ensuring timely monitoring and response.
Continuous Oxygen Analyzer:
- Installed for continuous exposure to gas, these analyzers are a staple in industrial settings, providing ongoing monitoring and control to maintain desired oxygen levels and optimize processes.
Oxygen Deficiency Analyzer:
- Critical for safety, these analyzers are specifically tailored to monitor oxygen levels in confined spaces, such as tunnels or control rooms, where fluctuations could pose risks to personnel and operations.
- Their role is paramount in ensuring a safe working environment.
Oxygen Analysis Methods
The oxygen analyzers in the industry utilize several measurement methods, which include
- zirconia,
- paramagnetic,
- optical,
- electrochemical types.
Each method presents its own set of pros and cons. It’s crucial to choose an oxygen analyzer based on the specific needs and conditions of your application. Below is an overview of each measurement method along with its advantages and disadvantages.
Zirconia Type Measurement System: Concentration Cell System
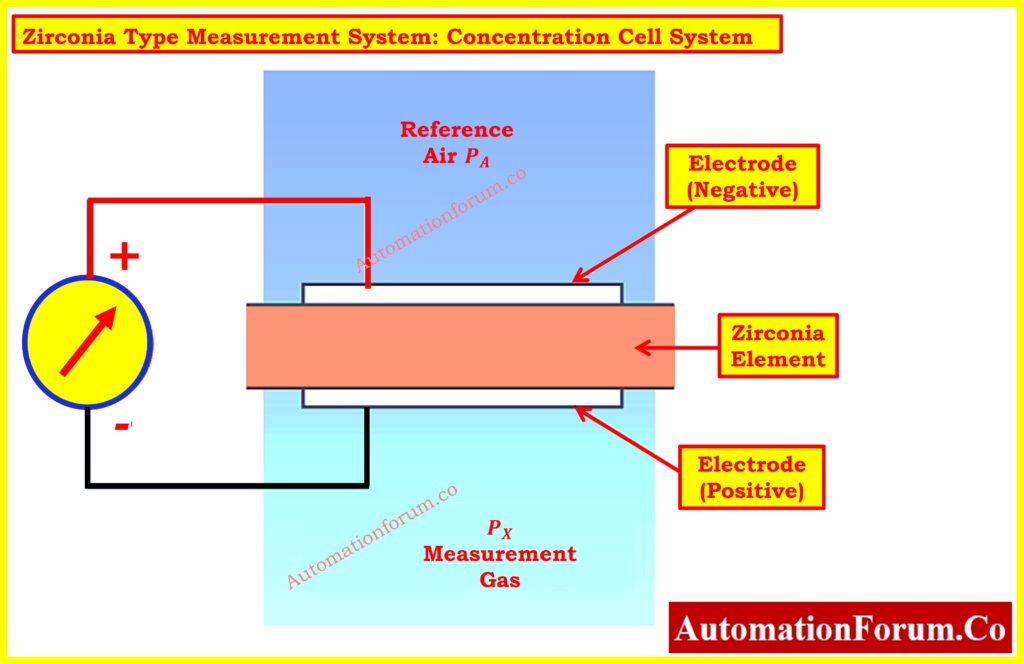
- The zirconia type measurement system utilizes the concentration cell system, leveraging the conductivity of oxygen ions in a solid electrolyte like zirconia at high temperatures.
- Porous platinum electrodes are affixed to both sides of the zirconia element, creating an oxygen concentration cell when heated.
- When gasses with varying partial oxygen concentrations interact with the zirconia surfaces, an electromotive force is produced between the electrodes, in accordance with Nernst’s equation.
- This force is directly proportional to the oxygen concentration.
Advantages:
- Direct installation in combustion processes such as boiler flues without the need for a sampling system.
- Faster response time compared to alternative methods.
Disadvantages:
- Potential for measurement errors if the sample gas contains flammable gasses, although combustion exhaust gasses typically pose minimal issues due to complete combustion.
Click here for Exploring Zirconia Oxygen Analyzers in Industrial Applications
Zirconia Type Measurement System: Limiting Current Type
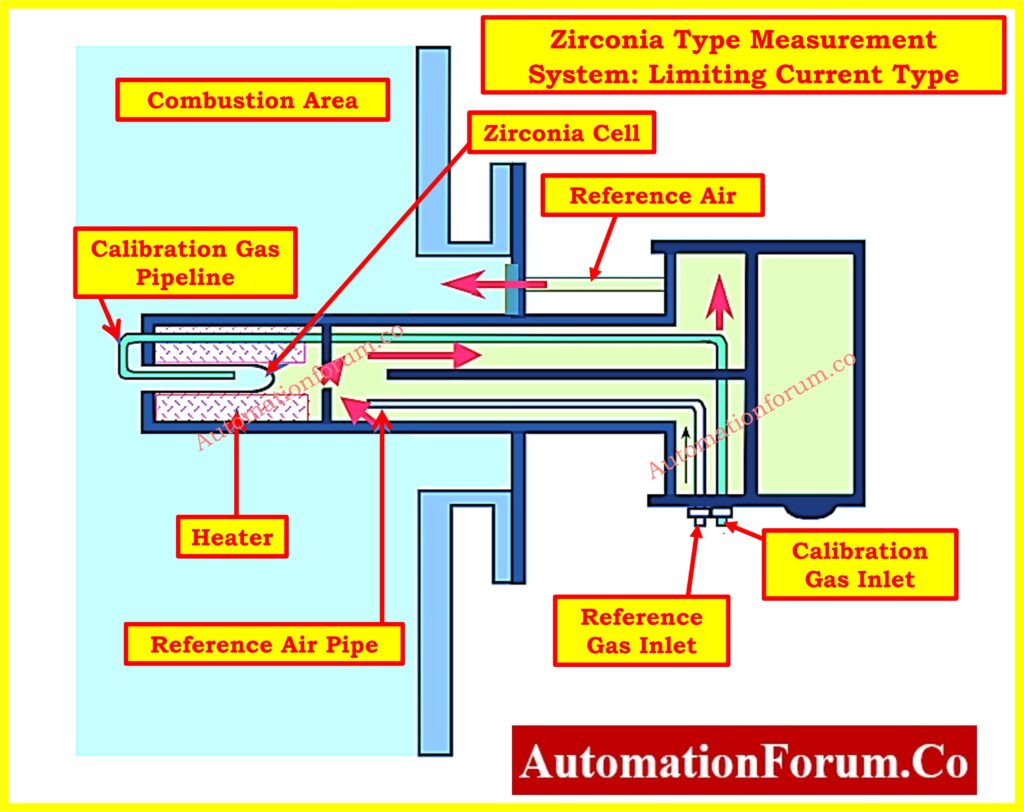
- In the limiting current type of zirconia measurement system, the flow of oxygen into the cathode of a heated zirconia element is restricted.
- This restriction causes a region where the current remains constant, even with increased applied voltage.
- This constant current is directly proportional to the oxygen concentration.
Click here for 9 Step Zirconia Oxygen Analyzer Calibration Procedure
Advantages:
- Capable of measuring trace oxygen concentration: This method is sensitive enough to measure even very low levels of oxygen.
- Calibration required only on the span side (air): Simplifies the calibration process, reducing maintenance needs.
Disadvantages:
- Potential measurement errors with flammable gases: Presence of flammable gases in the sample can lead to inaccuracies.
- Susceptibility to dust clogging: Dust accumulation on the cathode side can block gas diffusion holes, necessitating the installation of a filter in a preceding stage to mitigate this issue.
Click here for Step by Step Preventive Maintenance Procedure for Zirconia Type Oxygen Analyzer with Checklist
Magnetic Type Measurement System: Paramagnetic System
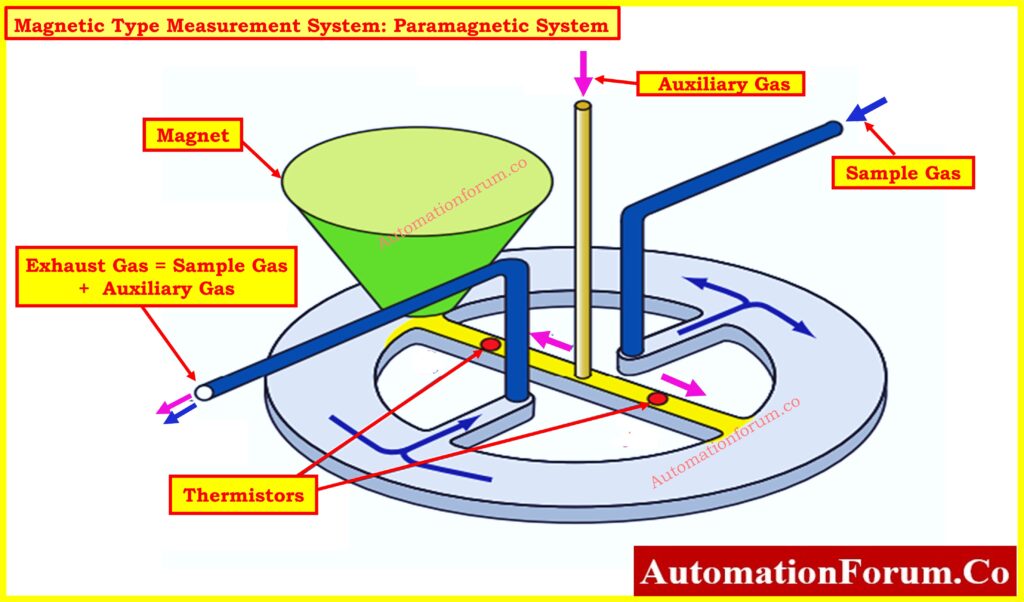
- The paramagnetic system is a method that exploits the paramagnetic property of oxygen.
- In this system, when a sample gas containing oxygen is exposed to a magnetic field, the oxygen is drawn into the field, causing a reduction in the flow rate of auxiliary gas in stream B.
- The difference in flow rates between streams A and B, resulting from the flow restriction in stream B, is directly proportional to the oxygen concentration of the sample gas.
- Thermistors determine the flow rates, converting them into electrical signals, with the difference computed as an oxygen signal.
Click here for Oxygen Analyzer Working Principle: Paramagnetic Type
Click here for 10 Step Oxygen Analyzer Calibration Procedure: Paramagnetic Type
Advantages:
- Measurement of flammable gas mixtures: Capable of measuring gas mixtures containing flammable components that cannot be measured by a zirconia oxygen analyzer.
- Compatibility with corrosive gases: Since there is no sensor in direct contact with the sample gas, the paramagnetic system can also measure corrosive gases.
- Fast response time: Offers a quicker response time compared to other magnetic types of analyzers.
- Resistance to vibration or shock: Exhibits greater resilience to vibration or shock than other magnetic systems.
Disadvantages:
- Sampling unit requirements: Requires a sampling unit tailored to the properties or applications of the sample gas.
Click here for Troubleshooting of Oxygen Analyzer : Paramagnetic Type
Click here for Step by Step Preventive Maintenance Procedure for O2 Analyzers : Paramagnetic Type
Optical Type: Tunable Diode Laser Measurement System
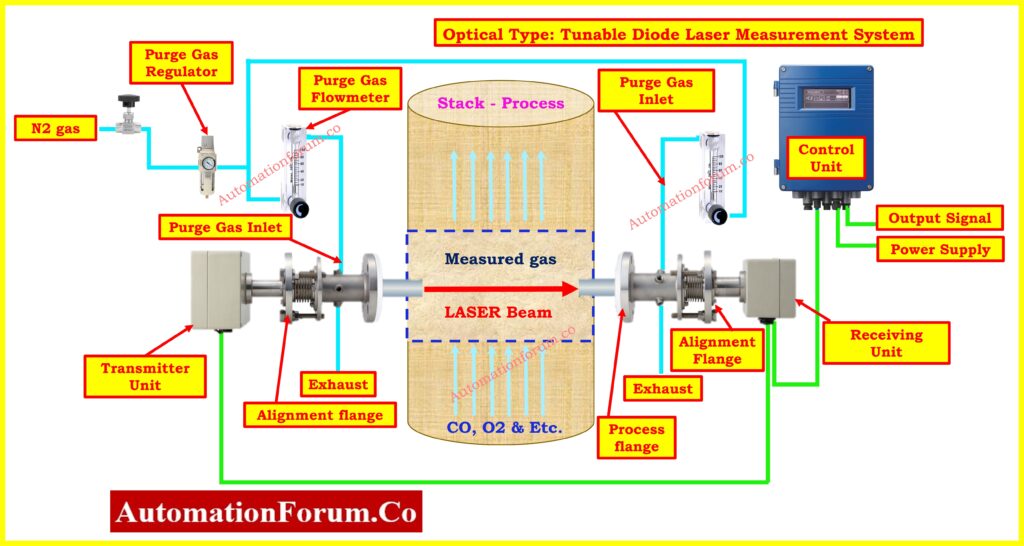
- The Tunable Diode Laser (TDL) measurement system relies on absorption spectroscopy principles.
- In this system, the TruePeak Analyzer operates by quantifying the amount of laser light absorbed as it traverses through the gas under analysis. A TDL analyzer typically comprises a laser emitting infrared light, optical lenses to focus the laser through the gas, a detector, and associated electronics for signal processing.
- Gas molecules absorb light at specific wavelengths, known as absorption lines, following Beer’s law.
TDL analyzers effectively utilize infrared radiation and adhere to the Beer-Lambert Law, expressed as
I = Io ·e-E ·G ·L
where I represents the radiation intensity post-absorption,
Io is the initial intensity,
E is the extinction coefficient,
G is the gas concentration, and
L is the path length.
Click here for Exploring Tunable Diode Laser Spectrometer (TDLS): Components, Principles, and Industrial Applications for Gas Measurement
Advantages:
- Versatile gas measurement: Capable of measuring various near-infrared absorbing gases, even in challenging process applications.
- Suitable for harsh conditions: Can operate at high temperatures, pressures, and in corrosive or aggressive environments.
- In-situ measurements: Most applications allow for in-situ measurements, reducing installation and maintenance costs.
Disadvantages:
- Requirement for flange installation: Installation of flanges is necessary on both sides of the process, adding to equipment complexity and cost.
Electrochemical Type: Galvanic Cell Type
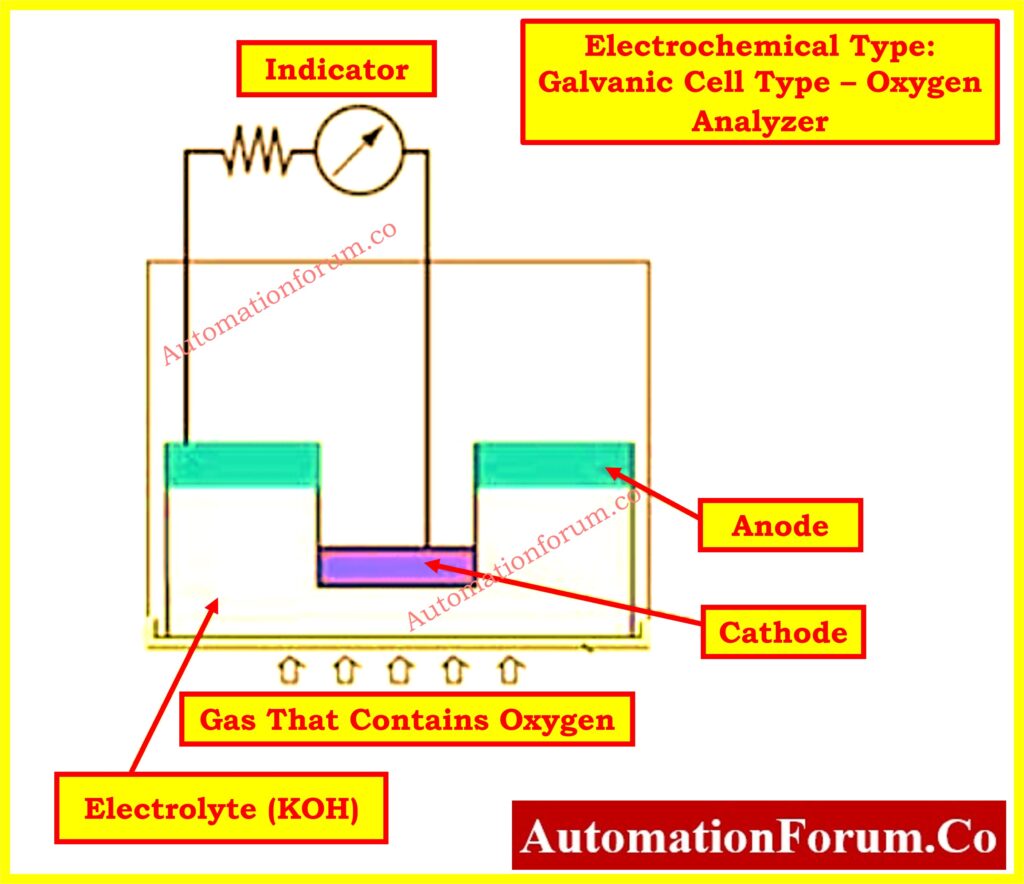
- In the galvanic cell type of electrochemical oxygen analyzer, oxygen is dissolved through a diaphragm into an electrolytic solution.
- This solution contains an anode (base metal) and a cathode (noble metal) positioned adjacent to each other.
- As oxygen passes through the diaphragm, a current proportional to the quantity of dissolved oxygen is generated.
- The amount of oxygen passing through the diaphragm is directly proportional to the partial oxygen pressure of the sample gas, allowing for the determination of oxygen concentration by measuring the current.
Advantages:
- Compact design: The detecting system can be made compact, enabling the measurement system to be available in portable or transportable forms.
- Cost-effectiveness: Relatively inexpensive compared to other types of oxygen analyzers.
Disadvantages:
- Limited cell life: The galvanic cell has a limited lifespan and deteriorates over time, even when not in use. Replacement is typically required approximately every year.
- Maintenance requirement: Regular replacement and maintenance are necessary to ensure optimal performance and accuracy.
Application Examples for Each Oxygen Analyzer
- Oxygen levels play a critical role in energy conservation, air quality management, safety protocols, and quality assurance across diverse sectors.
- Here are key applications categorized by the type of oxygen analyzer:
Application of Concentration Cell System (Zirconia Oxygen Analyzer)
- Package boiler combustion control in gas-fired systems.
- Combustion control in power generation boilers (gas-fired).
- Regulation of combustion in pulverized coal boilers.
- Control of hot stoves used in steelmaking.
- Monitoring of combustion exhaust gases in coke ovens.
- Management of heating and combustion exhaust gases in coke ovens for steelmaking.
- Control of low-oxygen concentrations in reheating and soaking furnaces for steelmaking.
- Detection of air leakage in sintering furnaces.
- Regulation of lime kiln combustion.
- Control of cement kiln combustion.
- Management of heating furnaces in oil refinery and petrochemical plants.
- Control of naphtha cracking furnaces.
- Monitoring and control of incinerator combustion.
- Oxygen concentration measurement in oxygen enrichment facilities.
- Monitoring of oxygen levels in exhaust gases from activated sludge process equipment.
Application of Limiting Current Type (Zirconia Oxygen Analyzer)
- Control of oxygen concentration in N2 reflow furnaces.
- Atmospheric control in semiconductor manufacturing equipment.
- Regulation of N2 and air purity in air separators.
- Prevention of oxygen deficiency.
- Control of oxygen concentration in glove boxes used for research, development, and parts machining.
- Monitoring and control of oxygen levels in experimental clean rooms for environment, fermentation, biochemistry, etc.
- Continuous measurement of flow gases during food packaging processes.
Application of Paramagnetic System Oxygen Analyzer
- Control of low-oxygen concentrations in CDQ plants for steelmaking.
- Monitoring and control of oxygen levels in gas mixtures containing flammable gases.
- Safety control to prevent explosions in various industrial settings.
- Measurement of trace oxygen concentration in various manufacturing processes.
- Quality control of city gas.
Application of Galvanic Cell System Oxygen Analyzer
- Prevention of oxygen deficiency in various industrial environments.
- Control of gas-fired package boiler combustion.
Application of Tunable Diode Laser Analyzer (TDLS)
- Monitoring and control of combustion in heating furnaces.
- Control of incinerator combustion.
- Process control in industrial applications.